Blade transport and safety - today
Safe transportation and storage of wind turbine (WTG) components require equipment that have sturdy yet flexible interfaces and a strong structure to protect the components.
Engineers therefore actively use various simulations, such as finite element modelling (FEM), during the design of transport equipment. These help to outline the load distribution on the interfaces and transport structures, ensuring they can withstand the expected loads whilst fully protecting the transported component.
But a recent field study gives firsthand insight into how these simulations can significantly misrepresent the true load distribution.
Benchmark study using field measurements
We placed load sensors within polyurethane WTG component interfaces on a blade clamp to measure loads during transport. We then analyzed the actual loads measured during transport and compared them with the expected loads from FEM simulations.
The FEM simulations expected high loads in the center part of the clamp, but the actual measurements showed that those areas experienced essentially no loads. Instead, the ends of the interfaces (pressure pads) experienced most of the stress.
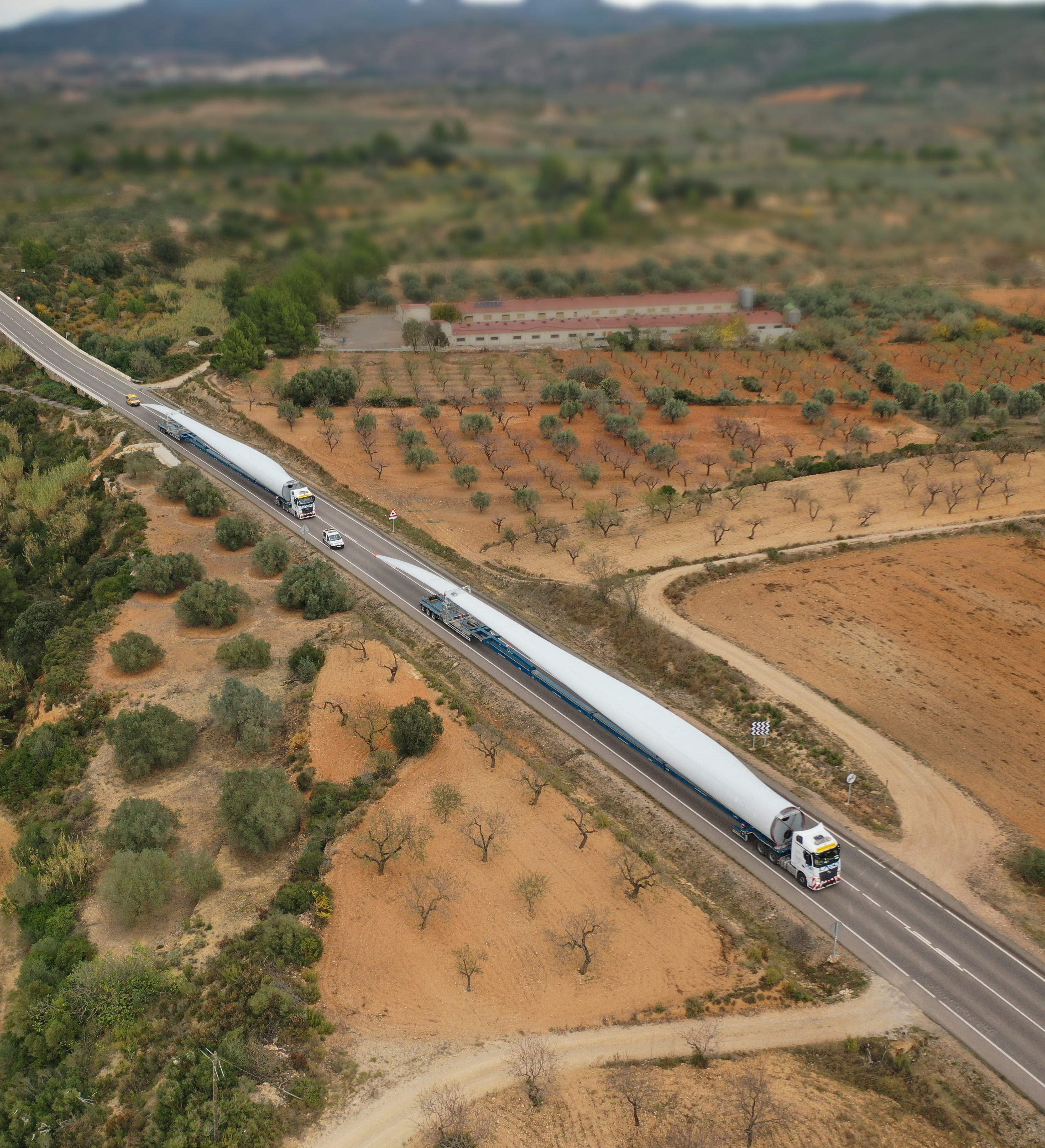
What do the results mean?
The results indicate that FEM simulations alone cannot be used to design durable transport equipment.
The analysis also implies that the industry might be designing suboptimal WTG components interfaces, that they are reinforcing transport equipment structures at the wrong places, and they fail to fully protect their wind turbine assets as their designs might fail early due to unexpected (and previously unidentified) excessive loads.
Future of transport equipment design
Only by understanding the true loads on the transport equipment can you and the industry lengthen the lifetime of interfaces and equipment, and fully protect the wind turbine assets.
With these insights, you can validate and optimize the design of WTG component interfaces and transport equipment.
These optimizations could lead to:
- more durable transport equipment,
- optimized structure reinforcements (e.g., no unnecessary welding and less steel),
- safer transport and storage of assets (e.g., avoiding blade damages), and
- reduced investments into repair or order of new transport equipment (longer lifetime of equipment means less damages, fewer repairs, and fewer new equipment orders).
Want to know more?
Contact our sales team to hear more about the study, and how we at Polytech can help you optimize your transport equipment for full protection.