Wind turbines are becoming larger to harness even more power from the wind. This trend we also see onshore, where longer rotor blades and increasing tip speeds, coupled with challenging weather conditions, bring the leading edge erosion problem more into focus.
Most of today’s modern onshore turbines have typically 60-meter-long blades, providing a rotor diameter of 120+ meters. Longer blades also mean higher tip speed, which can reach more than 250-300 km/h (80-100 m/s). Such speeds increase leading edge erosion on the blades as rain, hail, and other airborne particles expose the surface to extreme wear and tear when the turbine is spinning day in and day out.
8 out of 10 turbines erected between 2006-2017 require at least 3 meters of leading edge protection per blade as per Polytech's calculations based on DNV-RP-0573. High rainfall causes severe leading edge erosion.
Erosion reduces the blade's lifespan and performance, affecting the annual energy production (AEP) and increasing the maintenance cost. Leading edge erosion (LEE) is a well-known problem in the offshore wind industry, where leading edge protection (LEP) solutions are widely adopted. However, as onshore wind farms expand to more remote and harsh locations, they also face similar erosion challenges. More rainfall means more risk of LEE for the onshore blades. In other words, what was once an offshore problem is now becoming an onshore problem.
When do you need LEP?
You need LEP in almost all cases if you have a modern turbine with a tip speed above 80 m/s. Most onshore sites need extra LEP protection than just the standard out-of-the-factory coating to last a lifetime of approximately 25 years. But as tip speeds increase, climate change causes more severe rainfalls, and as site locations become more exotic, the need for LEP also increases to ensure the projected lifetime energy production.
Comparing LEP methods
Given the clear need to address this issue, the industry has explored several solutions:
1. Coatings: Specialized coatings, often made from polyurethane or epoxy, provide a protective layer against the elements. While they offer protection, they might require re-application over time due to wear, especially on today’s wind turbines where tip speed is significantly higher than five to ten years ago.
2. Paints: Protective LEP paints are a more straightforward solution. Limitations are similar to coating, so with today’s tip speed, paint is no longer sufficient over the lifetime of a wind turbine.
3. Tapes: Protective tapes, typically made of polyurethane or polymer, are applied to the blade's leading edge. They are replaceable, making maintenance easier, and often provide resistance to erosion. Some solutions require several replacements during the lifetime of the wind turbine.
4. Shells: Some are hardcovers. While they offer robust protection, they can be more complex to install. Some solutions might impact the blade's aerodynamics more than others.
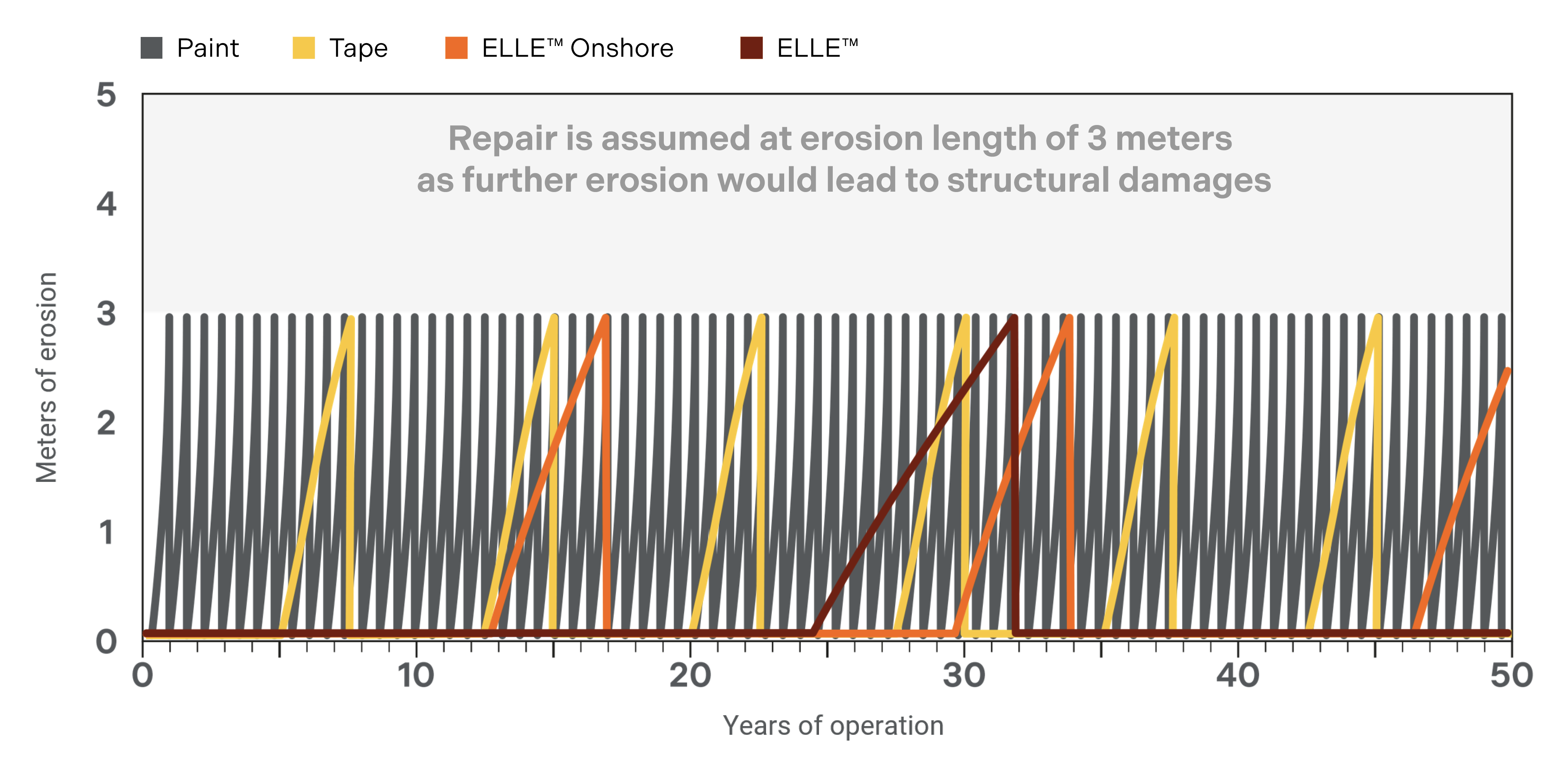
An example of erosion calculations from an onshore US site comparing Polytech’s ELLE® Onshore solution with standard coating and conventional LEP tape available on the market. The example shows that coating will start eroding instantly and require repair annually during the lifetime of the wind farm. Conventional tape LEP needs to be repaired three times during its lifetime, whereas Polytech’s ELLE® Onshore will last +15 years.
LEP solutions vs AEP Loss: the greater picture
When discussing the LEE, it is vital to understand its effect on AEP. When pristine and straight from the factory, a blade's leading edge offers optimal aerodynamic performance, ensuring maximum energy capture. However, as erosion takes hold, the surface roughens, disrupting the airflow and decreasing efficiency.
LEP solutions might introduce minor performance deviations compared to a brand-new blade. Yet, this slight reduction pales compared to the potential AEP loss over a turbine's lifetime if left unprotected. While an LEP might reduce AEP by a small fraction, untreated leading edge erosion can lead to significant reductions in AEP.
Read more about AEP studies carried out in wind tunnels and on operating turbines at the below links:
- Leading edge protection - the truth behind concerns
- Wind tunnel tests using ELLE®
- DNV report on turbine performance with ELLE®
- Data reveals stabilized energy production with ELLE®
Conclusion
Leading edge erosion is an undeniable challenge for the onshore and offshore wind energy sector. While protection methods might introduce minor efficiency reductions, they are a necessary trade-off when considering the AEP losses that unchecked erosion can introduce over a turbine's lifespan. As the industry grows, continued research and innovation in protection methods will be pivotal in ensuring wind energy remains efficient, reliable, and cost-effective. With the right solution, you, as owners of wind parks, will have the most optimal AEP over the turbine lifetime.