Lightning protection systems (LPS) for wind turbine blades come in various forms and designs. One of the many choices the OEMs face is between an internal and external down conductor in an LPS design.
LPS designs with internal and external down conductors
An LPS design with an internal down conductor includes many equipotential bonds within the blade to handle the inevitable current flow in the carbon spar caps. Such a system has traditionally also been favored as it enables an installation at the neutral axis of the main web and had therefore a natural bending capability together with the blade structure.
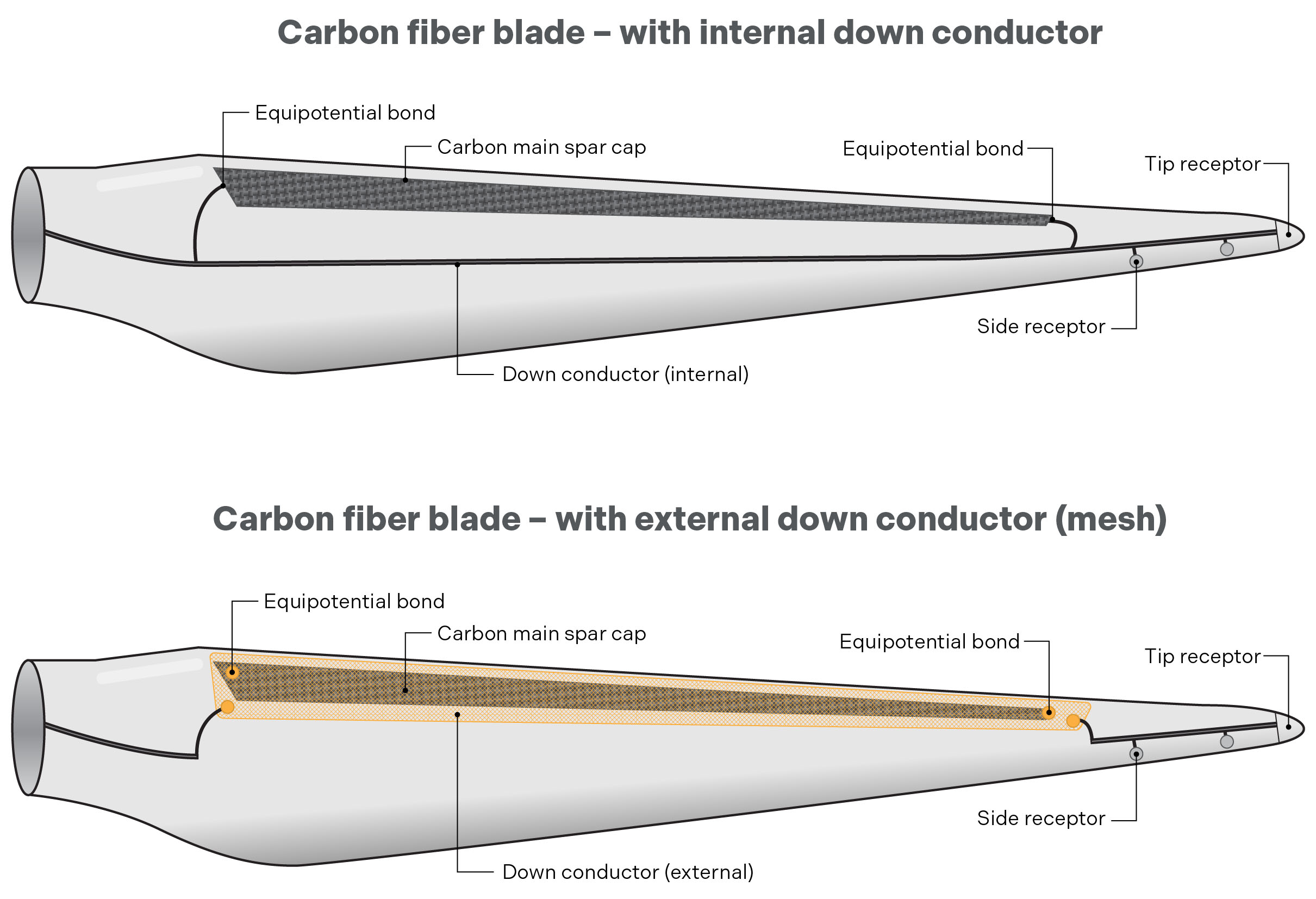
An LPS design with an external down conductor includes an expanded metal foil (otherwise known as mesh) that covers the carbon spar caps. This setup reduces the required number of equipotential bonds and offers direct strike protection (including protection against static electricity). In addition to this, modern mesh kits have increased strain capabilities, which means that they can effortlessly bend with the blade without the strain levels exceeding the design performance of the expanded metal foil.
As both lightning protection systems have major technologies differences, the question is how do they compare in performance?
Recent study investigating performance differences
Using electromagnetic simulation methods verified thoroughly according to IEC 61400-24 Ed2 Annex O, we analyzed the same blade design using an internal and an external down conductor in a carbon blade LPS. Our simulations showed major differences when it comes to the current flow in the blade. When using an external down conductor, average 83% lower peak current and 97% lower specific energy flows through the critical structural parts of the blade. And these results bring significant benefits to an LPS with an external down conductor.
In an LPS with external down conductor,
- the electric potential of the carbon main laminate is controlled by capacitive and inductive coupling to the mesh. This means there will be significantly lower voltage differences in the design.
- there is much lower current in the interface between the down conductor and the carbon. This allows you to reduce the number of equipotential bonds (and their sturdiness), which in turn reduces the weight and complexity of the blade.
- there is much lower current in the carbon pultrusions. This helps to avoid delamination between the pultrusions.
These simulation results prove that an external down conductor offers improved performance with a much simpler, more robust, and lighter design compared to an LPS with an internal down conductor.
Reach out to Søren F. Madsen, Head of Electrical & Mechanical Engineering to learn more about these simulations and the implications for your wind turbines.